How to Use Water Based Print on T-Shirts In 7 Easy Steps
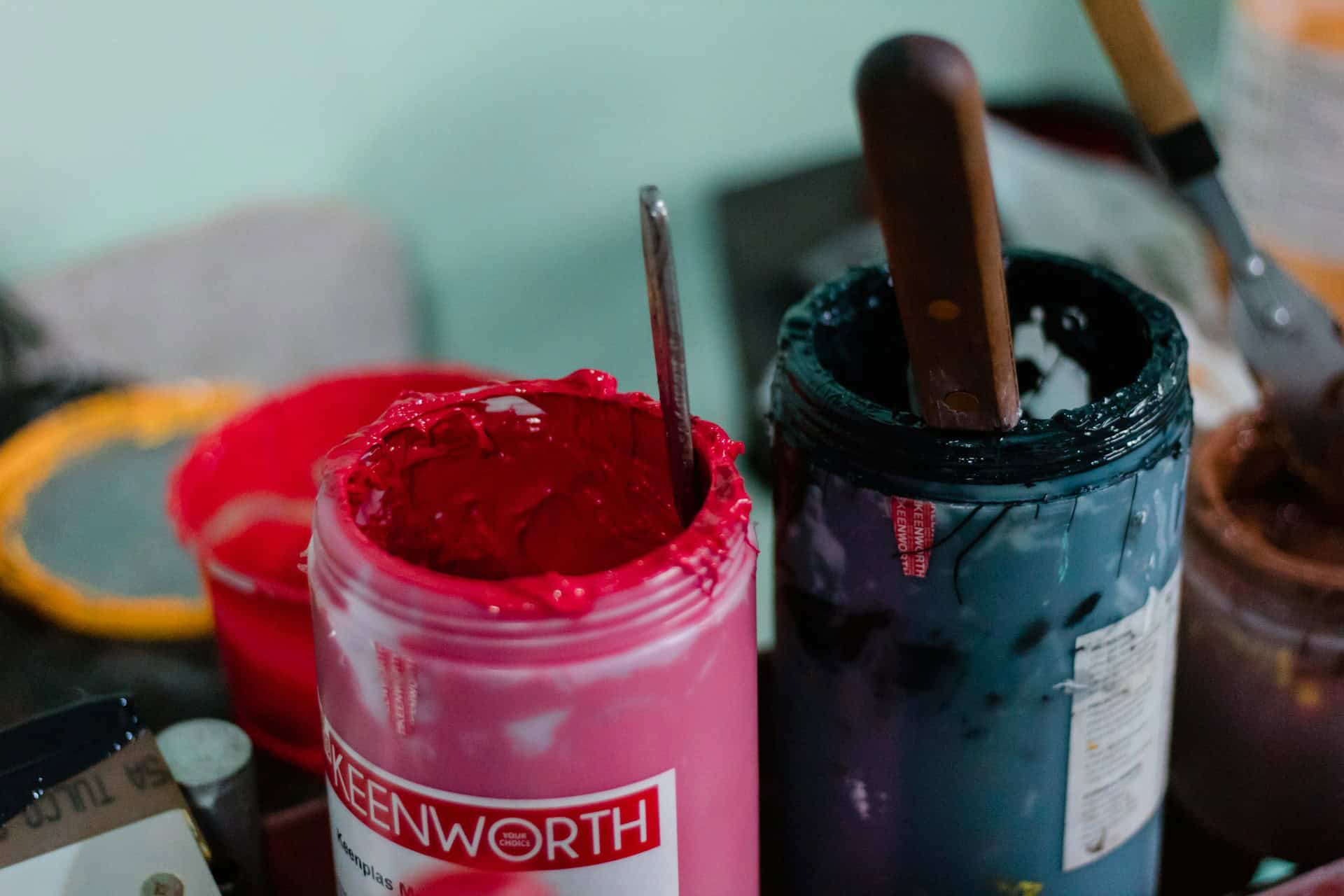
Share The Love:
Unlock the eco-friendly and creative world of screen printing with water based print inks and you’ll gain a competitive advantage. 86% of shoppers view sustainability as a desirable objective.
However, about half (48%) are unsure of how or where to acquire such items and 42% are puzzled about what criteria define clothes as sustainable. Now is the time to make your processes public.
Whether you’re a hobbyists or custom apparel businesses, learning this method can enhance your designs with vibrant colors and a soft feel, all while satisfying the growing need for eco-friendly clothing.
What is Water Based Print?
Screen printing with water-based ink involves transferring a design onto a t-shirt using a mesh screen, water-based ink, and a squeegee. This process is celebrated for its ability to produce detailed graphics with a soft-to-the-touch finish.
Unlike plastisol inks, which sit on top of the garment, water-based inks soak into the fabric, creating a print that moves with the shirt. This technique is a great choice for those looking to produce high-quality prints that are both pleasing to the eye and the environment.
The reason water-based printing stands out is its compatibility with both light-colored garments and dark garments. When it comes to dark fabrics, discharge inks, a specialized form of water-based inks, can be utilized to remove the shirt’s dye and imprint the design in vibrant colors.
This ensures that each printed garment retains the breathability of the fabric, making screen printed shirts with water-based ink equally comfortable to wear and visually appealing.
Why You Need to Know How to Screen Print with Water-Based Ink
Eco-friendly alternatives to traditional printing methods have become increasingly important in the industry, and screen printing with water-based ink answers this call brilliantly.
This method not only reduces the environmental impact due to its lower VOC (Volatile Organic Compounds) content but also elevates the end product with a softer feel that customers love.
The versatility provided by water-based screen printing allows you to create garments with long-lasting prints that don’t crack or peel over time.
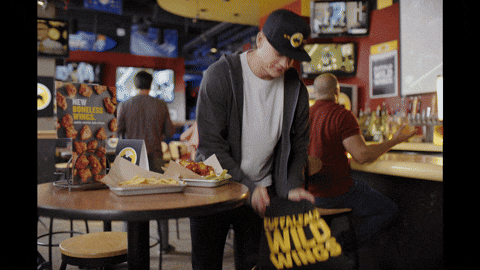
This durability aspect, combined with the method’s inherent eco-friendliness, positions screen printing with water-based ink as an essential skill for anyone serious about producing top-tier apparel.
The shift towards sustainable practices in the fashion industry further underscores the importance of mastering this technique, making it invaluable for both new entrants and established brands.
7 Tips For Screen Printing Water Based Ink on T-Shirts
The art of water-based ink printing is rather straightforward. With our comprehensive guide, you’ll learn each step of the process from start to finish.
Whether you’re looking to make a personal statement with a custom t-shirt or step up the quality of your apparel brand, implement the following to start on the right foot.
1. Prepare Your Workspace
Ensure your space is clean and organized to facilitate a smooth printing process. The preparation phase is crucial, as any contaminants can interfere with the quality of your prints.
Also, considering water-based inks can dry out quickly, having a well-organized workspace helps in managing inks efficiently and keeping everything within easy reach to expedite the printing process.
2. Choose a Finer Mesh Count Range & Dark Inks
Start with Dark Inks
To get started, print water based ink only on your garments using dark inks. This method is quite straightforward if you’re new to water based printing.
Why Water Based Ink is Easier
Water based ink is thinner than plastisol, making the process simpler in some ways. You’ll need to use a higher mesh and print wet-on-wet instead of flashing between layers.
The benefit? The thin ink doesn’t pick up as much on the back of the screen, allowing you to move the squeegees faster. Typically, the ideal mesh count for these inks ranges from 160-230.
Emulsion Matters
It’s crucial to use an emulsion suited for water based inks. Without it, the stencil can deteriorate, ruining your print run. Be sure to check your emulsion compatibility to ensure your prints come out perfect.
The selection of screens, squeegees, and the right type of t-shirts also play a significant role. Opt for a screen with the appropriate mesh count depending on the viscosity of the ink.
3. Use Light Color Fabrics
Best Practices for Water-Based Screen Printing
Water-based screen printing relies on dyes or pigments suspended in water. The most vibrant color results appear when printed on a lighter color base. Let’s break this down a bit. Picture diluting some paint in water and then trying to use it on a black piece of paper.
You’ll see the print design, but they won’t stand out as much as they would on white paper. The reason? Light-colored base allows the dyes to show their true vibrancy. For instance, if you were to print a bright yellow design on a white shirt, the colors would pop.
However, that same yellow might appear dull or muddied on dark blends. This is due to how water-based inks interact with the fabric. They soak into the fibers rather than sitting on top, making the underlying color crucial for achieving the desired look.
Useful Tip:
Always test your design on a sample fabric before committing to a full print run. This helps ensure that the colors appear as intended, especially when working with intricate designs or specific shades.
4. Prepare Each Design
Choosing or creating the perfect design involves understanding how different elements will translate onto fabric using water-based inks. Given the inks’ slightly thinner consistency and how they soak into the fabric, opting for designs that complement this characteristic will ensure accurate and striking results.
5. Gather & Prepare Your Screens
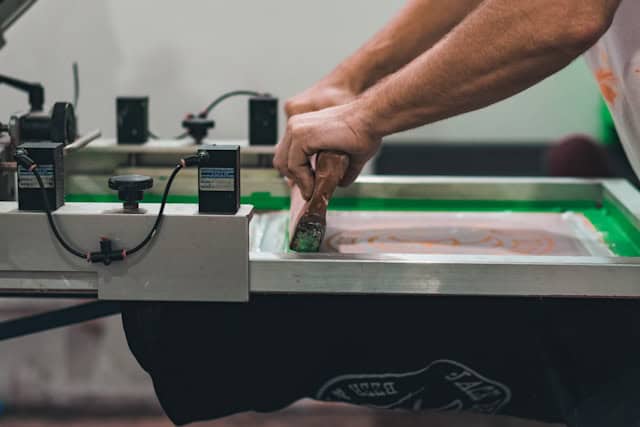
The preparation of your screen, including the application of the stencil and making sure the screen is properly tensioned, sets the foundation for a successful print run.
Using a high-quality emulsion ensures that your designs are accurately transferred and that the screen withstands the pressure of repeated use, particularly important when working with water-based inks that require thorough screen cleaning after each session.
6. Start the Printing Process
The printing process with water-based inks requires attention to detail and precision in squeegee pressure and angle.
Unlike plastisol, water-based ink requires slightly more force and a sharper angle to push the ink into the fabric properly.
Ensuring even coverage and maintaining the right amount of ink on the screen can make all the difference in achieving vibrant and consistent prints.
7. Cure the Print
One effective way to cure water-based ink without a forced-air dryer is by utilizing a regular dryer along with Warp Drive. Warp Drive chemically cures water-based ink within 48 hours. Here’s how to use it:
- Mixing the Additive: Add Warp Drive to your ink at a ratio of 1.5% by weight.
- Printing as Usual: Print the ink onto your garment as you normally would.
- Drying Process: Use your preferred curing method. Warp Drive will ensure the ink cures chemically, even without special equipment.
Difference in Curing Methods
Water-based inks cure differently from plastisol. When the water component evaporates, it leaves the pigment behind. To make sure the pigment bonds correctly to your fabric, all water must evaporate.
Follow Manufacturer’s Guidelines
Always adhere to the curing specifications provided by your ink manufacturer. Many recommend a forced-air dryer for optimal results. Gas conveyor dryers with forced-air options are often more effective than electric ones for this purpose.
If you’re using a regular dryer, set the correct temperature and timing to facilitate proper evaporation of water from the ink. Testing a few samples can help you fine-tune the process and achieve the best results.
8. Clean-Up Your Work Area
Water-based inks allow for an easier clean-up process compared to plastisol inks, as they can be cleaned with water. However, it’s essential to promptly clean your screens to prevent ink from drying and clogging the mesh.
A thorough clean-up contributes to the longevity of your screens and ensures they’re ready for your next project.
Troubleshooting
Screen printing with water-based ink can sometimes present challenges, such as ink drying in the screen or difficulty in achieving vibrant prints on dark garments.
Applying a retarder can help keep the ink from drying too quickly, while experimenting with different discharge ink formulas and underbases can improve vibrancy on darker fabrics.
Final Tips and Considerations
To master the art of screen printing with water-based ink, it’s beneficial to experiment with different fabric types and ink formulations.
Understanding the behavior of various inks on different textiles not only enhances your flexibility as a printer but also allows you to offer a broader range of products to your customers.
Additionally, stay updated with the latest industry trends and innovations to keep your ecommerce store or shop ahead of the curve.
Key Considerations Before Screen Printing with Water-Based Ink
Understanding the nuances of water-based ink, such as drying times and proper screen preparation, can greatly impact the quality of your prints.
Always ensure the ink is properly mixed and the screens are correctly prepared to avoid common issues like blotching or fading.
Next Level Strategies to Master Water-Based Screen Printing
Venturing beyond basic techniques to explore advanced methods and ink mixing can open up new avenues for creativity and unique effects.
Custom color mixing and experimenting with additives can help you create specialty inks that set your work apart, offering your clients something they can’t find elsewhere.
Alternatives to Water-Based Ink Screen Printing
While water-based inks offer numerous benefits, other methods like plastisol ink printing, DTF, and Direct to Garment (DTG) offer alternatives for different needs and preferences.
Each method has its unique advantages, and selecting the right one depends on the project’s specific requirements and the desired outcome.
Wrapping Up
Through dedication and practice, screen printing with water-based inks can become an essential part of your repertoire, allowing you to offer high-quality, environmentally friendly apparel.
The satisfaction of producing soft, detailed prints that stand the test of time is worth the effort, making every project a rewarding experience.
Frequently Asked Questions
What are the main benefits of using water-based ink over plastisol?
Water-based inks are more eco-friendly and provide a softer finish on fabric, enhancing the wearability of printed garments.
Can water-based ink dry out during the printing process?
Yes, water-based inks can dry quickly. Keep the ink moist and work efficiently to prevent this issue.
Do I need special equipment for screen printing with water-based ink?
The basic equipment is similar to other screen printing methods, though considerations for drying and curing times may require additional tools.
How do I prevent ink from bleeding on the fabric?
Proper screen tension, appropriate mesh count, and precise pressure during printing can help prevent bleeding.
By adhering to the outlined tips and techniques, you’re well on your way to mastering the craft of screen printing with water-based ink, ensuring your designs not only look spectacular but also stand the test of time.
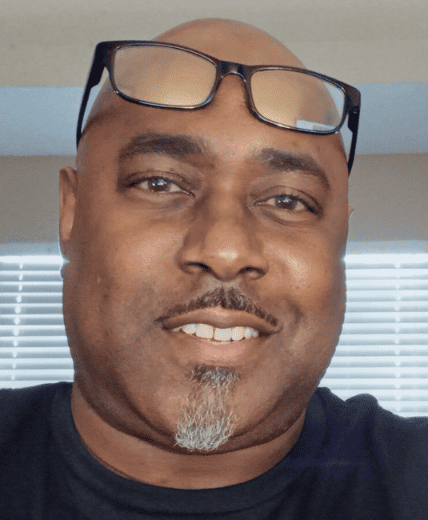
Ken Jones
Ken empowers small business owners and entrepreneurs to scale productivity through innovative content creation, strategic planning, and cutting-edge technology. He’s passionate about helping businesses thrive in the digital age.